The friction material on the driven plates was laughable at best. One of my driven plates was total shit. The teeth had stripped completely but luckily it appeared the input shaft was as good as could be expected. I found the holes in all three plain metal plates ovaled far beyond any specs I could find.
I decided to order all five plates, new springs, and screws from my "local" ural parts/service guy. Anyone in the Chicagoland area who needs parts or a knowledgeable repair guy, his name is Bob, email is uralbob@att.net. He's out in the suburbs, Glen Ellyn to be exact. He was even nice enough to salvage a clutch bolt for me too since i had to drill the head off of one screw to get the clutch out as can be seen in the photo below. Someone before me decided to use non-hardened allen head bolts and one was completely rounded. I don't have a press but I removed/installed it in a very inappropriate and potentially damaging manner that need not be written.
I butchered my perfectly good, brand new drive plates after reading what Mr. Cobb has done to help dissipate heat in hard conditions. I will go one step further, cutting expansion slots when I remove the clutch assembly for inspection later. For now, cooling holes should be fine. I would recommend using a drill press if attempting this process but with steady hands and care, any old drill will do.
I went to the hardware store and purchased three 8mm x 1.0 x 50mm bolts and nuts to match. For anyone not familiar, 8mm is the size(width) of the bolt, 1.0 is the thread pitch, and 50mm is the length. They could be a bit shorter, but worked just fine. Put one nut on each bolt and run it all the way up to the head of the bolt. Now, on to the installation of my new clutch.
Step 1: Place the six springs into the holes in the flywheel. I used a piece of newspaper to hold them in place which will most likely burn up or somehow disintegrate with time and should do no harm.

Step 2: I stacked the five clutch plates in order and placed the alignment tool through the two driven plates and into the plate closest to the springs. I aligned the bolt holes on the three metal plates then lifted the assembly up to the flywheel and fitted the springs into the holes in the first plate. Be sure all of the springs are in their holes and thread the three nut/bolt combos into the flywheel using every other screw hole in the metal plates. I couldn't really take a picture at this point since my hands were full but the picture step 4 should tell the story well enough.
Step 3: After threading the bolts into the flywheel, spin the nuts so they are just starting to apply pressure on the cover plate. I did not use washers here, but it may be a good idea and I probably will on the next go round.
Step 4: Tighten each nut 1/2 turn to gradually compress the springs evenly. Repeat this process until the first plate is touching the clutch bolts. It may be necessary to guide the plate onto the bolts by nudging it this way or that. This picture shows the first plate on the clutch bolts with the second plate about to go on. Again, a little wiggling may be needed to line up the bolts with the holes.
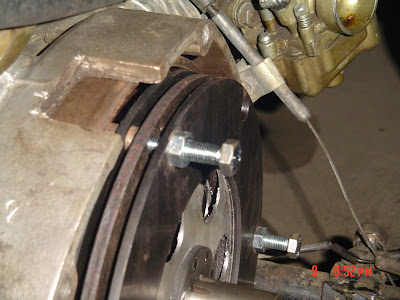
Step 5: Keep turning each nut 1/2 turns to fully compress the springs until the cover plate rests against the clutch bolts.

Step 6: Install three clutch screws in the open holes in the plates. Most say to use blue loc-tite on the screws then punch the edges once all screws are in and tight. I will try just loc-tite for now and decide if I need to punch them too when I inspect the clutch in a few hundred miles.

Step 7: Remove the three nut/bolt combos and replace with the remaining clutch screws, again using loc-tite and punching the edges if you so desire.
Step 8: Open beer and drink.
*
**
***The alignment tool is simply an old input shaft cut off beyond the groves. Borrow or make one if you can to make life much easier when you put the transmission back in.
*
**
***To avoid damage to the clutch screws, use an impact driver to install/remove the screws. This may be difficult to impossible with the engine still in the frame unless you remove the rear tire and fender.
*
**
***Removal instructions and pictures will be added in a few hundred/thousand miles assuming I remember to take pictures when the time comes.
No comments:
Post a Comment